Wireless Pendant
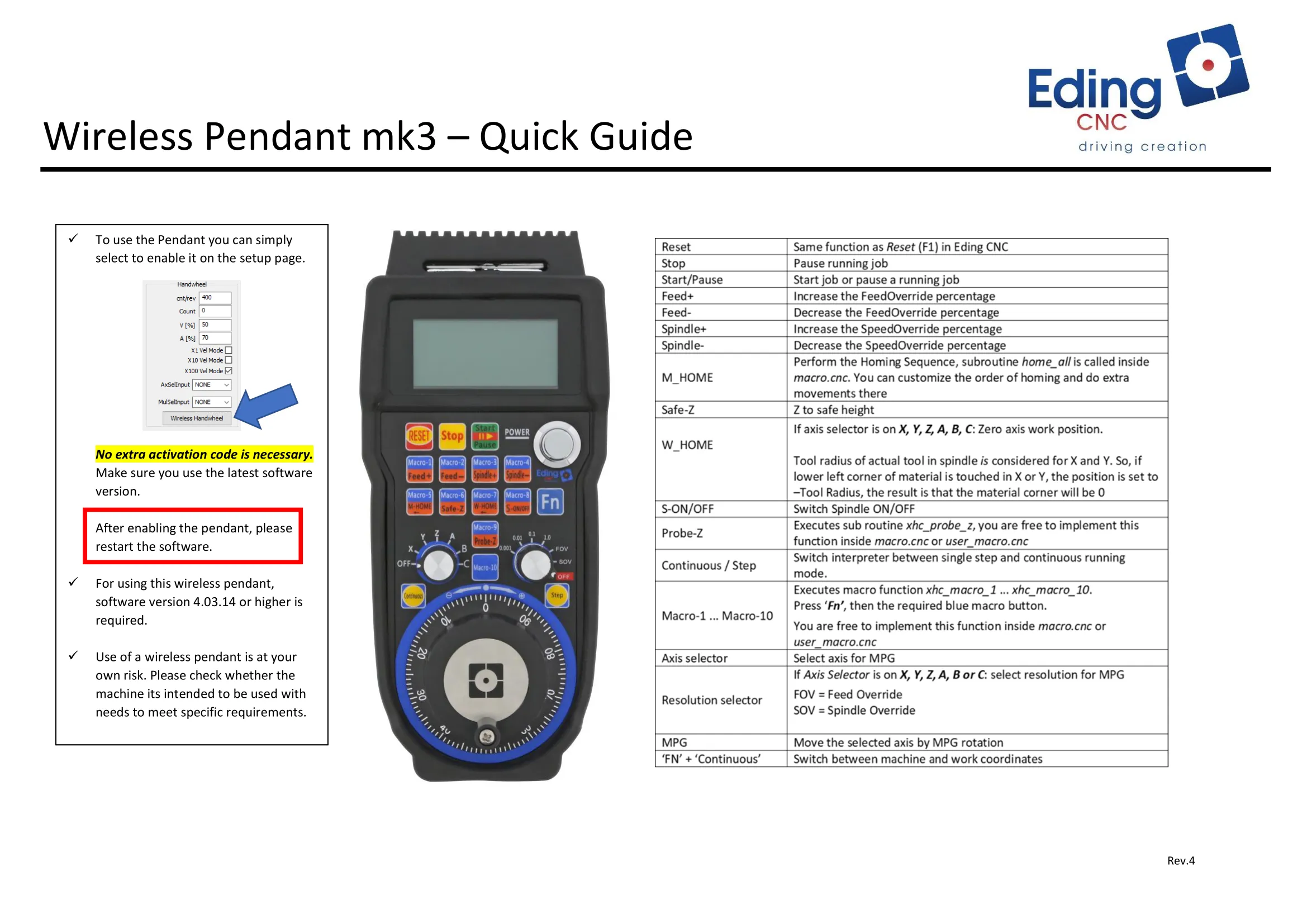
The Wireless Pendant is really useful for positioning and zeroing and other functions on the machine, it is not really suited for milling because there is no feel of the force, the milling bit will break easily. The movement may not be entirely smooth. The pendant is easy to use, and of course wireless. It operates with batteries; the batteries will last about 1 month in normal operation. Due to the resolution of the Pendant MPG, 100 pulses/revolution lower acceleration must be used to get smooth movement.
The movement with the wired Pendant can so smooth motion with higher acceleration. The wired Pendant has 400 pulses/revolution.
Please note, the rules for safety about using wireless pendants can vary per country. The usage of this pendant is at your own risk.
Put 2 AA batteries in the Pendant. When the pendant is not used it is recommended to switch it off, so the batteries are saved. Connect the USB RECEIVER to the USB port of the PC. The USB receiver must have a free line of sight to the pendant. This means it will not work well if the USB receiver is built into a metal cabinet and the pendant is outside.
In Setup 2/2, you can find the button for setting up the pendant.
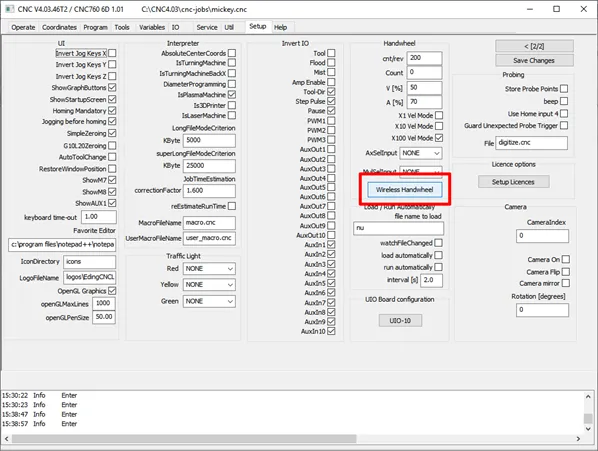
After clicking, you will see an overview of the supported pendant models. Select the correct model. It is likely that you need to select "Model 3".
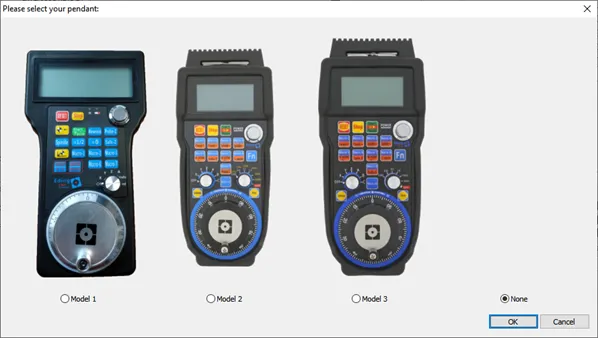
Once the use of the wireless pendant has been enabled, (re)start the software. An additional program that communicates with the pendant is also started, it looks like the image below and shows information from the pendant:
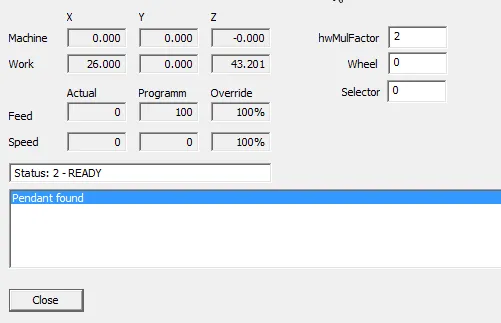
It shows “Pendant found” if everything is OK. You can leave this running in the background, it will perform the Pendant functionality for Eding CNC.
The Pendant itself has a timeout; this is to preserve the batteries. It is important to know that after a few seconds of not pressing a button or not rotating the MPG, the Pendant goes to a sleep situation where there is no longer communication with the PC. In the sleep situation, the positions on the display no longer match the actual machine position and the software goes automatically out of hand wheel operation. When a button is pressed or the MPG is rotated, it goes back to normal operation, and the positions are updated.
Button | Function |
---|---|
Reset | Same function as Reset (F1) in Eding CNC |
Stop | Pause running job |
Start/Pause | Start a job or pause a running job |
Feed+ | Increase the FeedOverride percentage |
Feed- | Decrease the FeedOverride percentage |
Spindle+ | Increase the SpeedOverride percentage |
Spindel- | Decrease the SpeedOverride percentage |
M_HOME | Perform the Homing Sequence, subroutine home_all is called inside macro.cnc. You can customize the order of homing and do extra movements there |
Safe-Z | Z to safe height |
W_HOME | If axis selector is off: G0 X0 Y0 If axis selector is on X, Y, Z, A, B, C: Zero axis work position. Tool radius of actual tool in spindle is considered for X and Y. So, if lower left corner of material is touched in X or Y, the position is set to –Tool Radius, the result is that the material corner will be 0 |
S-ON/OFF | Switch Spindle ON/OFF |
Probe-Z | Executes sub routine xhc_probe_z, you are free to implement this function inside macro.cnc or user_macro.cnc |
Continuous / Step | Switch interpreter between single step and continuous running mode. |
Macro-1 ... Macro-10 | Executes macro function xhc_macro_1 ... xhc_macro_10.Press ‘Fn’, then the required blue macro button. You are free to implement his function inside macro.cnc or user_macro.cnc |
Axis selector | Select axis for MPG |
Resolution selector | If Axis Selector is on X, Y, Z, A, B or C: select resolution for MPG If Axis Selector is on OFF: change FeedOverride |
MPG | Move the selected axis by MPG rotation |
Pendant macro buttons "Macro-1" through "Macro-10" have their own macro .
They call a macro subroutine from macro.cnc file. You can define subroutines xhc_macro_1 through xhc_macro_10 in your macro.cnc file.
Add a subroutine with the right name in the macro.cnc file to use this feature:
For example, if we add this to the bottom of the macro.cnc file:
then subroutine user_1 (User macro 1) will be called when we press Fn+Macro-1 on the wireless pendant.
The resolution (cnt/rev) of the MPG is 400. In some older copies, the resolution may be 200. If you have a machine with high acceleration it may be noticed that the move is not smooth. This is because every count of the MPG gives a small displacement and if your machine has high acceleration the displacement is already done when the next count pulse is read. This can be smoothed out by setting the speed and acceleration percentage lower, such that the movement is smooth enough for normal MPG operation. The parameters are in the setup of the software:
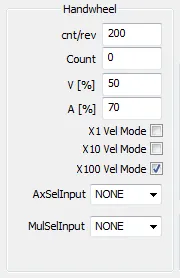
- Cnt/Rev: The number of counts of the hand wheel for one revolution, usually 400 for most CNC hand wheels.
- Count: Counter for wired hand wheel, not used for the XHC Pendant, normally 100 pulses/rev.
- V[%]: Percentage of velocity from the selected axis, this is the maximum velocity the axis will move when using the hand wheel.
- A[%]: Percentage of acceleration from the selected axis, this is the maximum acceleration the axis will move when using the hand wheel.
- X1..X100 Vel Mode: In velocity mode, the most important is that the movement stops immediately when the rotation of the hand wheel stops. The position of the hand wheel will not be maintained if velocity mode is on. The position of the handheld is maintained if velocity mode is off. This also means that the axis may not immediately stop if the handwheel rotation stops. When turning beyond the limits of the axis, you have to turn back the hand wheel the same amount before the axis starts moving again. In our experience is that it works best to use velocity mode at X100 only.
These parameters allow you to tune the motion behavior such that it has acceptable smoothness and speed.
USB
Please use a direct USB 2.0 port on your laptop. USB hubs may cause issues.
Try a different computer
Before contacting your dealer, it is appreciated if you try the device with a different computer first, to rule out that the handwheel itself is defective.
Software does not recognize the handwheel
Please try to enter safe mode of your Windows computer and try to run the software then.
If the handwheel is recognized in safe mode, it is possible that there is some kind of software on the computer that interferes with the handwheel receiver.